With intelligent drying and heat pump drying towards more sustainability
Drying of organic food is characterized by empirical approaches when it comes to product quality and system design. Alternative drying conditions and improved system control can improve the product quality and reduce the energy demand for the producers.
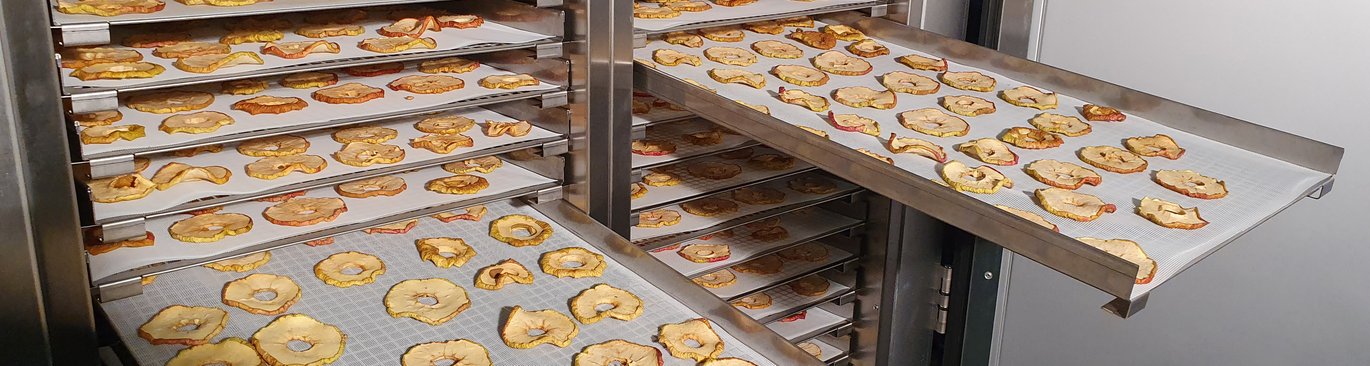
In WP 2 of the SusOrgPlus project, SINTEF, together with Innotech Ingenieursgesellschaft mbH and University in Kassel, we have therefore established a flexible SusOrgPlus drier in which industrial drying conditions can be tested under controlled laboratory environment. This enables to test different products, qualities and optimize different drying conditions and systems before the concept is established in the industry.
The SusOrgPlus drier has an industrial size of 30 kW, which corresponds to a batch drier for e.g. 100 kg of organic apples. The main drying conditions like temperature, humidity and air velocity can be controlled and optimized by e.g. controlled uptake of fresh air. SINTEF has developed a heat pump system based on the natural refrigerant R744 (CO2) which can be used as alternative primary energy supply. This enables to reduce the carbon emissions of the drying process to almost zero and at the same time reduce primary energy consumption since the driers waste heat is reused.
Senior Researcher Michael Bantle from SINTEF explains:
"The main challenge was to integrate a heat pump in a batch drier which has a high energy demand in the beginning and low energy demand towards the end of drying. We decided to install a thermal energy storage for process heat as well as process cooling in the form of water tanks. Doing so we can shut down the heat pump once the energy storage is charged and operate the drier on its own waste heat".
With this concept it is expected to reduce the primary energy consumption by at least 50 percent.
Additional features of the drier are that a camera as well as different sensors for monitoring drying conditions are used to upload real time information for the smart control and optimization system which is in the cloud. The expectation is that a self-learning cloud-system can optimize the drying process without the help of human manpower. The SusOrgPlus vision is hereby that different driers are connected to the same cloud and that e.g. manufacturer in Germany can automatically get optimized drying conditions based on own results but also process experience from other driers.
SINTEF will establish the SusOrgPlus drier as part of its permanent laboratory infrastructure HighEFFlab. https://www.sintef.no/projectweb/highefflab/
Contact: https://www.sintef.no/en/all-employees/employee/?empId=4503