Heat pump drier for organic products offers new possibilities
The SusOrgPlus project developed and demonstrated the concept of heat pump drying for the organic sector. The technology allows better product quality and faster drying by a smart control system of the drying conditions and reduces the energy demand by re-using the drying energy
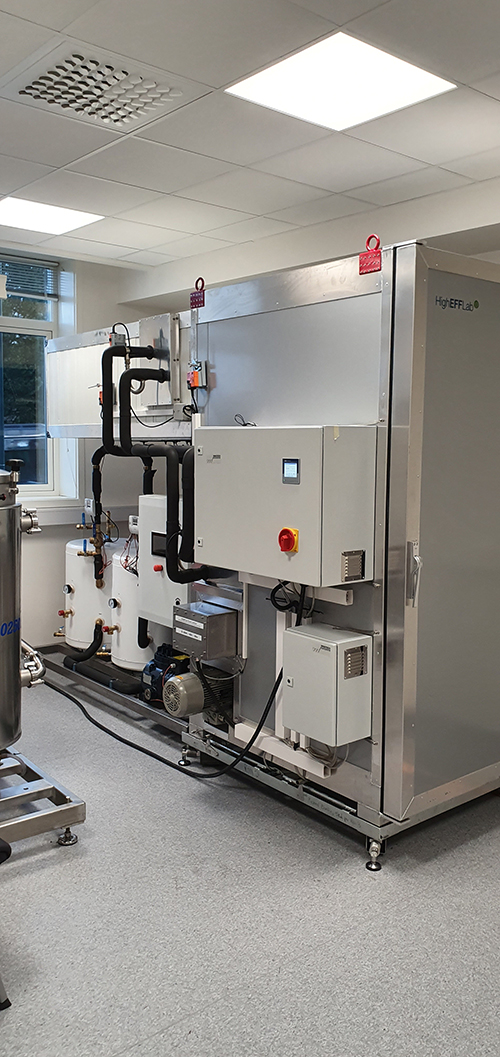
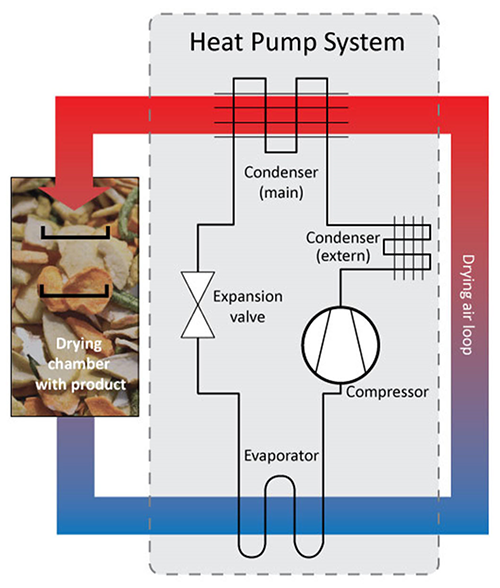

Dried organic fruits and vegetables are a growing market and enables organic producers to process products with higher value addition. However, drying is a time consuming and energy demanding process in which the product quality is defined by the drying conditions. Most driers use hot air to remove the moisture of the product. With increased drying temperature the product dries faster but the product quality (defined e.g. through colour change or shrinkage) will reduce. Therefore, a fine economic balance needs to be found for every product in which the processing conditions and time are chosen with respect to achievable quality.
The humidity of the drying air is, especially at lower drying temperatures, as important for the drying speed and product quality as the drying temperature itself. However, many control systems only allow the adjustment of the air temperature and consequently the humidity is a result of the local ambient conditions of the production site. This can result in effects which can spoil whole product batches when e.g. the batch is dried on a hot and humid summer day.
More advanced drying systems use controlled ventilation of fresh air which is mixed with re-circulated drying air. This allows a dynamic control of an air-flap between the ambient and the drying chamber. Especially the required heating of the drying is energy intensive which makes drying costly while at the same time significant amounts of climate gases are emitted.
Through the SusOrgPlus project SINTEF (Norway) together with Innotech Ingenieursgesellschaft mbH (Germany) has equipped an industrial drier with a heat pump. The heat pump has two main functions: the refrigeration side is used to de-humidify the drying air while the "hot" side is used to re-heat the drying air to the required temperature. Doing so the system can remove more moisture in a shorter time while the primary energy consumption of the system is reduced. For organic apples the drying time was reduced by 25 percent, while the energy consumption was reduced by 40 percent. Or in other words: a significant increase in productivity was achieved at lower specific energy consumption.
Another feature of the system is the dynamic process control which measures continuously the product colour, shrinkage and temperature and adjusts the drying conditions (temperature, humidity, air velocity) to the optimum. In the next step the controller will be connected to a database in order to self-optimize the drying conditions and learn from drying tests which were performed using other driers and at different locations. This work is conducted in a collaboration between SINTEF, Innotech and Uni Kassel.
The SusOrgPlus project is funded via the ERA-net CORE Organic Cofund based on funds from participating countries and funding from the European Union and aims to improve the drying processes for organic products in terms of sustainability and product quality.
https://www.sintef.no/en/drying-of-biological-material/
https://www.sintef.no/globalassets/project/highefflab/onepager_heat-pump-drying.pdf/
Author
Michael Bantle (Phd), SINTEF Energy Research, Michael.Bantle@sintef.no,
www.sintef.no/en/all-employees/employee/
Editor: Karin Ullven / Design: Christine Dilling